|
Repair vs Replace - Part 3
Key concepts for better decision-making
This is Part 3 of a paper was presented to the Asian Maintenance in Mining Conference, Lombok, Indonesia on 15 March 1999
Author : Sandy Dunn
5. Inhouse vs Outsource - the implications
For most mining operations, there are three options available for component rebuilds:
- Retain (or establish) an inhouse component rebuild capability
- Outsource component rebuilds to the Equipment Manufacturer's local agent (PT Trakindo, PT United Tractors, Hastings Deering, Westrac, Gough & Gilmour or others)
- Outsource component rebuilds to the Equipment Manufacturer (Caterpillar, Komatsu or others)
Deciding which of these options to adopt is clearly a long-term strategic one - and therefore should be carefully considered. We would recommend that this decision be considered along two separate dimensions:
- What is the strategic importance of the activity to your organisation? In other words, which option provides the greatest opportunity for long-term strategic competitive advantage in your company's chosen marketplace, and
- Which option provides the service in the most cost-effective way - not just in terms of costs, but also including service levels, responsiveness and all the other factors that go to make up a quality service offering.
After considering these issues, the ultimate decision regarding whether or not to outsource the activity may be determined in accordance with the following two by two matrix.
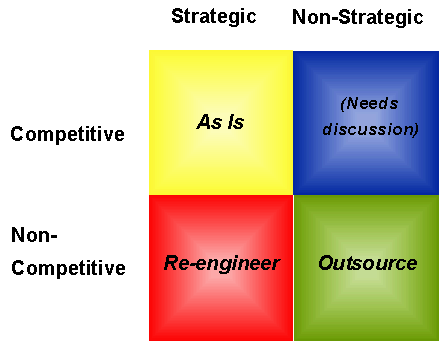
The outsourcing decision is a worthy subject for another conference paper, and we will not go into the decision making process in too much detail here - except to make the following comments:
5.1 Strategic Importance
The primary determinant of long term competitive advantage in the mining industry is price - the lowest cost producer (per tonne, pound, or ounce of output) will always be guaranteed market share. Consideration of the strategic importance of major component overhauls, therefore, should revolve its importance in terms of impact on the unit cost of production. The major questions to ask are:
- Is it an expensive activity?
- Does it significantly impact on equipment downtime, and therefore output (or required capital investment)
5.2 Competitiveness
The major considerations in determining the competitiveness of an in-house versus an outsourced component rebuild function are:
- Work Quality - can an inhouse facility rebuild items to equivalent or better quality than an outsourced facility?
- Labour Productivity - will inhouse workers be as efficient as those at an outsourced facility?
- Labour rate - Is inhouse labour cheaper or more expensive than that provided by a contractor?
- Component turnaround time - can components be repaired and/or rebuilt more quickly at an inhouse or an outsourced facility?
The first two items have been covered in earlier discussions, but it is worth expanding on the last two points.
5.2.1 Labour Rate
Since the decision to outsource is essentially a long-term, strategic one, we must be sure to include in our assessment of the relative costs of the inhouse vs outsource option, the likely impact on overhead costs. While, in the short term, these costs are fixed (we are unlikely to significantly change the number of accountants in the company, nor the amount of company-provided accommodation, nor the number or size of workshops and other buildings), in the longer term, a decision to outsource may lead to the deferral or disposal of expenditure on other overheads. Therefore, an allocation of costs for relevant overheads must be included in our inhouse costing. This is generally included in the direct labour rate.
To be able to accurately estimate the appropriate allocation of overhead costs, full Activity Based Costing analysis is preferable, but more approximate estimates can be made with considerably less effort.
The other adjustment that should be made, so that labour rates can be accurately compared with external sources, is to adjust the labour rates to take account of the fact that some shopfloor labour will always be spent performing non-direct activities, such as safety meetings, training etc. In a contract environment, the contractor cannot charge his client for these activities, but instead incorporates an allowance for these activities in his direct labour rate. To ensure that we are comparing "apples with apples", this similar adjustment must be made for the inhouse costs.
5.2.2 Component Turnaround time
An on-site rebuild facility, whether inhouse or outsourced, may enable faster turnaround of components for rebuild. Time spent transporting components is reduced. This may enable to organisation to reduce the total number of components held in stock, and therefore reduce the capital investment in components that are held in spares. If you consider that typically, the holding cost of spare parts is around 20% of their total value per annum (including opportunity cost, obsolescence and storage costs), this could amount to substantial savings.
5.3 A competitive marketplace?
There is one other strategic consideration in the outsourcing equation. If you outsource, does a competitive marketplace for the rebuilds exist? It is fair to say that component manufacturers hold considerable influence over the rebuild marketplace, as they are the custodians of the technical knowledge required for rebuilding components. They are often the only possible source of spare parts for these components. If you outsource your component rebuilds to the manufacturers, are you creating a monopoly situation, which will result in you being unable to either return the function inhouse, or find an alternative, competitive supplier tobid for this work? Even if you are, does this matter greatly?
This issue is currently being overcome by making it a condition of sale of the original equipment that the equipment suppliers provide ongoing maintenance of their equipment at pre-agreed rates - the so-called "power by the hour" contracts. This recognises the reality of the marketplace - that the only time that a mining company has any power to influence ongoing maintenance costs (if it is outsourced to the supplier of that equipment) is at the time that they are making the original purchase decision for that equipment.
6. A final critical issue - Management Control
Of course, all the best plans go awry if there is no power or control over repair vs replace decision making at a shop floor level. There must be clear guidelines for supervisors and planners to adhere to, and the management information systems must be in place to ensure that these guidelines are being adhered to.
7. Data Requirements for effective decision making
It is clear from the previous discussion that, for effective decision making, a range of quantitative information is required. This may include:
- The downtime associated with a component replacement
- The labour hours associated with a component repair or replacement
- The cost of labour (including allocation of overheads and adjustment for the amount of indirect time spent by shopfloor employees)
- The expected life and reliability of a new component compared with an overhauled component
- The cost of downtime
The challenge, in most organisations, is finding reasonably accurate data in each of these areas. Based on our experience, it is often difficult, if not impossible, in many mine sites (despite the fact that most of them engage in component tracking), to determine the expected life and reliability of a new component compared with an overhauled component. Accurate labour costing, both in terms of labour rate, and accurate labour hours associated with component exchanges and rebuilds, is also notoriously difficult to find.
Yet without this information, repair vs replace decisions will continue to be made. These are often the wrong decisions, and often have extremely expensive results.
Is accurate information available in your organisation to support the repair vs replace decision?
|
8. Conclusion
In conclusion, I hope that you have gained the following key points from this discussion.
- Repair vs Replace decisions have expensive consequences, yet are often made without full and proper analysis - "rules of thumb" are often inappropriate.
- The appropriate tool for accurate decision making is to use a Life Cycle costing approach..
- .but accurate data is often not available to support this decision tool
- The most accurate decision model is useless, without effective management control to ensure that it is being appropriately applied.
The next step is clear. If you want to save $2 million per annum - get control of the repair vs replace decision.
Previous Page
Copyright 1996-2009, The Plant Maintenance Resource Center . All Rights Reserved.
Revised: Thursday, 08-Oct-2015 11:54:38 AEDT
Privacy Policy
|
|